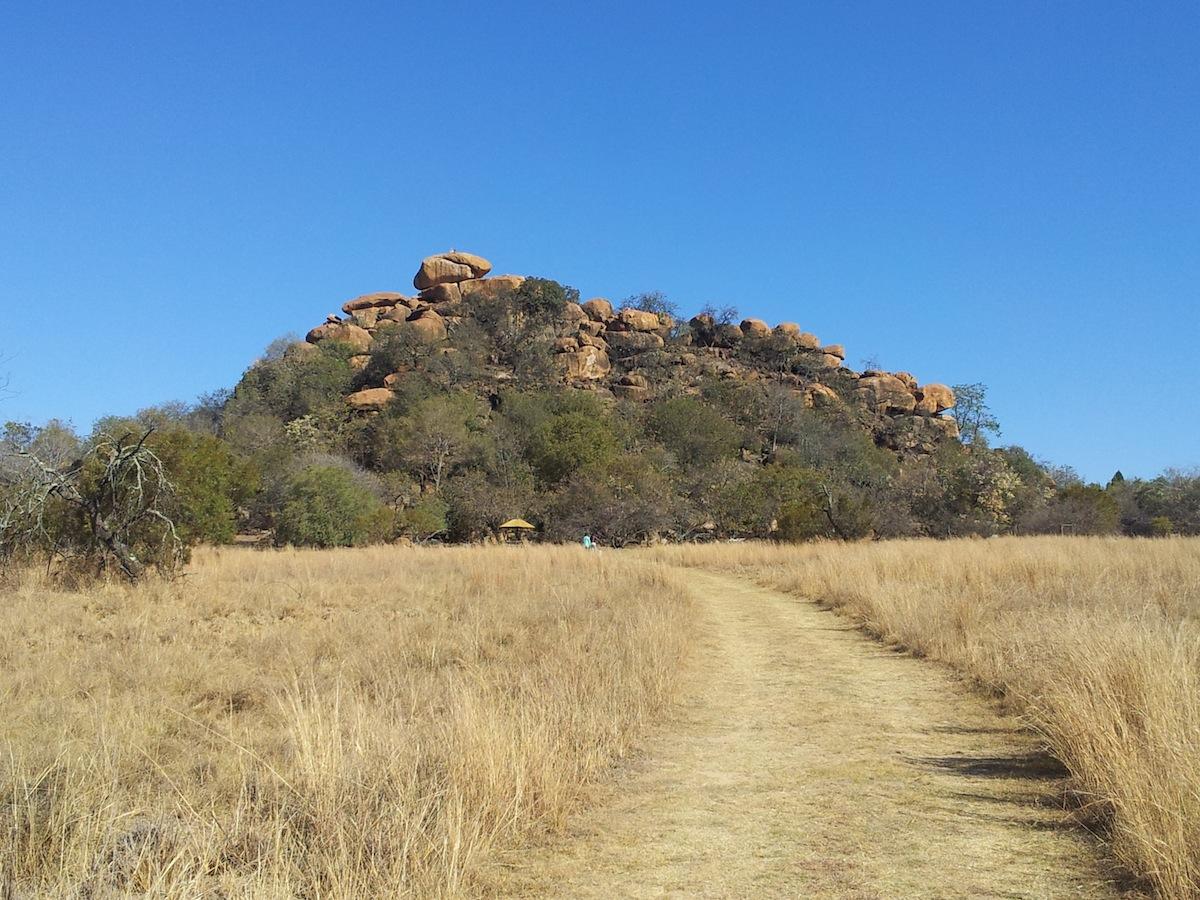
Disclaimer: Any views expressed by individuals and organisations are their own and do not in any way represent the views of The Heritage Portal. If you find any mistakes or historical inaccuracies, please contact the editor.
To the north of Johannesburg lies a hill of great historical, archaeological and geological importance. In the article below Lilith Wynne explores the archaeological aspects of the Lone Hill site. The article first appeared in the 1988 Journal of the Sandton Historical Association, two years after Professor Revil Mason made his 'discovery'.
Right in the middle of Sandton is a site which could become an important part of our community life and a focal point of education. According to Professor Revil Mason, Director of the Archaeological Research Unit of the University of the Witwatersrand, this discovery represents one of the finest Iron Age Smelting and Forging sites in Southern Africa, and may even be the most complete.
Regrettably, the area is scheduled for town house development. Fortunately, soon after the discovery, building and development was stopped by the owner, Mr Oswald Buckner. Sponsored by the Sandton Council, the Archaeology Unit with Professor Mason and Mr Robbie Steel moved onto the site to make a detailed investigation. It soon became apparent that in Sandton we have a site of national historical importance, one that merits all efforts to preserve it.
Development around the area today (The Heritage Portal)
Excavations begin
The first excavation showed a large iron smelting area, dated by samples of charcoal to about three hundred years ago. Fragments of pottery on the site can be attributed to Sotho/Tswana speaking peoples. The ornamental patterns and styles of the pottery are similar not only to those from +- 60 other Iron Age sites in the Transvaal, but are also similar to patterns still made by the Sotho/Tswana today.
Later, following the drilling of fifty-three test holes, a huge granite anvil was found. The boulder had a crust of iron and clear cut grooves, indicating exactly where the tools were hammered into shape. Actual hammerstones of hard igneous diabase rock were lying nearby, further proof of iron processing activity. This made Lonehill unique, in that it preserved not only evidence of the first process of extraction of iron from the ore, but of the second process, that of the production of iron weapons, ornaments etc.
Until a few years ago, archaeologists thought that furnaces alone were involved in the production of iron. It is now known that the furnaces were just the first part of a long and complex process of refinement of the basic iron 'sponge' which the furnace produced.
At the top of the 'lone hill' (The Heritage Portal)
Why at Lonehill?
The Lonehill site was chosen by the Tswana for smelting because of the abundant ferricrete along the Jukskei Spruit. Ferricrete is a concentration of iron salts in the soil, originating in the underlying granite. An important factor, too, in the siting of the forges was the air currents that rise up the slope from the valley.
Geological Blue Plaque at Lonehill (The Heritage Portal)
Precise layout
From the excavations it was noted that there was also an interesting relationship in the spacing of the furnaces. The remains of the three furnaces showed that they were exactly 1,10 metres apart and 1,20 metres long. Although the reason for this is not known, precision must have been of the utmost importance.
Precision of spatial layout can also be illustrated from details of a settlement site at Broederstroom which has been dated 1000 years earlier. At Broederstroom one can still see the settlement layout by the precise positioning of boulders that once supported raised floors. Undoubtedly, ritual would have been another factor at Lonehill which would have been associated with the success of the whole operation. Historical records of iron production in Zimbabwe, that continued into the 20th century make reconstruction easier and give support to the archaeological evidence.
Similar furnace and living floors have been found on Melville Koppies in Johannesburg, and two wooded ferricrete producing areas formed an important 'factory' that supplied the Iron Age settlements of the grasslands further south. In the Klipriviersberg, a days walk south from Lonehill, were Johannesburg's first farmers, who had cattle, sheep and goats, and who grew millet, which would have been traded for the iron weapons, ornaments and farm implements from both Lonehill and Melville.
A lone hiker at Lonehill (The Heritage Portal)
The manufacturing process
The ferricate would have been placed in the furnace with charcoal and heated to 1000 Centigrade, then sealed with clay to retain heat and hasten the fusion of the ore. It would have taken two of the acacia or olive trees in the area to produce 100kg of charcoal. Then, clay blowpipes directed the airblast horizontally into the furnace on either side. These blowpipes had slim bellows attached to them and these had to be continuously operated by teams of men for six to seven hours.
The resultant small pellets of iron-rich slag were then raked out, cooled and carried upslope to the forges for resmelting. After several hours, only a small handful of good iron would be produced.
Professor Mason feels that Lonehill should be developed as a dynamic display of the early mining skill on the Witwatersand.
The Lonehill Koppie has already been fenced for protection (there are remains of early hut floors there too). Professor Mason feels that if the area between it and the river could be retained, preserved and documented, then Sandton would have a unique facility of national importance.
Comments will load below. If for any reason none appear click here for some troubleshooting tips. If you would like to post a comment and need instructions click here.